- Manufacturing
- 14.10.2022
Managing the Manufacturing Process in ERPs
A step-by-step guide to the implementation of Manufacturing Automation
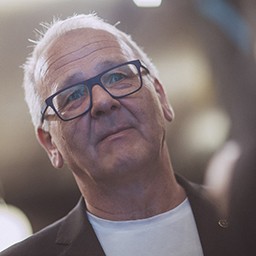
Dr. Andreas Maier
14.10.2022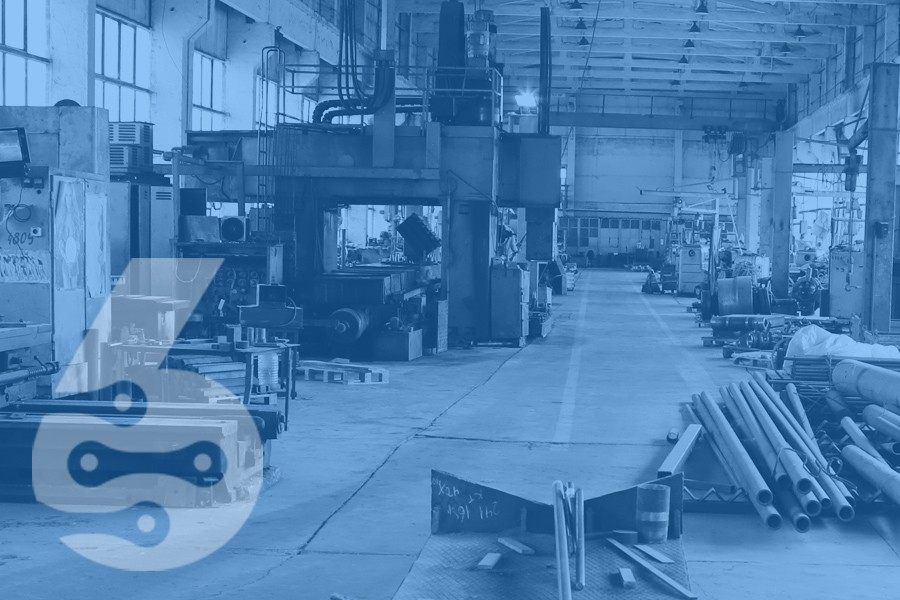
“ Automation is no longer just a problem for those working in Manufacturing. Robots will replace physical labor; AI and software will replace mental labor. “
Enterprise Resource Planning (ERP) systems are integrated software solutions that help businesses manage the vital components of their operations, including product development, Manufacturing, supply chain, shipping and logistics, customer relationship management (CRM), and finance.
An ERP system consolidates all of these business functions into a single, comprehensive software solution that can be accessed by authorized users from anywhere in the organization. This centralized access to information and data allows businesses to streamline their processes and improve their efficiencies.
While ERP systems vary in features and functionality, they all share the same primary goal: to provide businesses with a complete overview of their operations and make informed decisions that will help them optimize their performance.
The Benefits of ERP
Enterprise resource planning (ERP) systems are popular in medium and large manufacturing organizations because they offer several benefits, including:
- Managing the manufacturing process from start to finish in one system.
- Improved visibility into the business, with real-time data on inventory levels, production schedules, and costs.
- Reduced paper usage and improved accuracy with electronic documentation and automated data collection.
- Increased efficiency by automating material requisitioning, order entry, and invoicing.
- Reduced lead times and enhanced customer satisfaction with better planning and execution of production schedules.
- Improved capacity through better utilization of machines, materials, and labor.
- Greater agility in responding to changes in customer demand or production plans.
How ERP manages the Manufacturing Process
ERP systems help manage and control the manufacturing process by integrating all data and processes from raw materials to finished products. ERP provides a single source of data accessed by all departments, which helps streamline the manufacturing process and improve communication and collaboration between departments.
The Planning Process
ERP systems streamline the planning process by integrating all relevant data and presenting it in a way that makes it easy to see what needs to be done and when. By managing the manufacturing process in ERPs, production managers can see which products need to be produced, how many units of each product are needed, what resources are required, and when the product needs to be delivered.
Information resulting from the planning process can be used to create a production schedule that ensures that all products are delivered on time and that the correct number of units is produced. ERP systems also enable tracking progress and identifying potential bottlenecks to take corrective action if necessary.
The Scheduling Process
In an ERP system, the manufacturing process is typically subdivided into two main types: production and discrete.
- Production processes combine materials to create a new product, such as in the food and beverage industry. Production scheduling is responsible for managing the production process and ensuring that products are produced on time and to specifications.
- Discrete processes are those where each individual product is made separately, such as in the automotive or electronics industries.
The main advantage of using an ERP system to manage the manufacturing process is that it allows businesses to have visibility into all aspects of the manufacturing process. Increased visibility means that companies can identify bottlenecks and potential issues before they occur, which can help to improve efficiency and reduce costs.
The Execution Process
To correctly manage the manufacturing process, manufacturers must consider numerous factors such as resources, capacity, competition, and customer demand. Enterprise resource planning (ERP) systems provide the necessary tools and capabilities to manage these factors and optimize the manufacturing process.
The execution process in an ERP system includes the following steps:
- Planning: The first step is to develop a plan that covers all aspects of the manufacturing process, including production goals, schedules, and budgets.
- Scheduling: The next step is to create a schedule detailing when each manufacturing task or process should be performed. This schedule should take into account all available resources, both human and machine.
- Production: Once the schedule is finalized, production can begin. ERP systems provide tools to track progress and identify any bottlenecks or areas of waste.
- Quality Control: Quality control is an essential part of the manufacturing process, and ERP systems provide tools to help ensure that products meet specifications.
- Delivery: The final step is to deliver the product to the customer. ERP systems can track inventory levels and generate shipping documents as needed.
Implementing ERP in your Manufacturing Business
An ERP, or enterprise resource planning system, is a software solution that helps businesses automate and manage their daily operations. A manufacturing business has different needs than other types of companies, so it is vital to choose an ERP system designed for Manufacturing. In this article, we will discuss the benefits of ERP for manufacturing businesses and how to implement it in your industry.
Defining Your Goals
ERPs are complex systems, so it's essential to define your goals before you embark on a project to implement one. Doing so will help you determine which features are most important to your business and which ones are secondary. Defining goals will also help you set a budget and timeline for the project. It is always wise to involve a consultant with prior experience in the field of Manufacturing automation to get the best estimates based on experience in the field of Manufacturing.
Here are some things to consider when defining your goals for an ERP implementation:
- What are your overall business goals? How do you expect an ERP system to help you achieve them?
- What processes do you need to streamline or automate?
- What information do you need to track? How do you need to be able to access it?
- Who will use the system, and what training will they need?
- What are your budget and timeline constraints?
Assessing Your Current Processes
Evaluating your current manufacturing processes is the first step in deciding how to implement ERP in your business. You'll need to closely examine every aspect of your production, from raw materials acquisition to finished product shipping, and document each process in detail. Once you comprehensively understand your current manufacturing workflow, you can identify areas where ERP would be most beneficial.
Key factors you should consider when assessing your processes:
- Efficiency: How quickly and easily can raw materials be converted into finished products? Are there any bottlenecks or inefficiencies in the process?
- Flexibility: How easily can the process be adapted to changes in demand or circumstances? Can the process be scaled up or down as needed?
- Quality: Are finished products meeting customer expectations? Are there any issues with defects or waste?
- Cost: How much does it cost to produce each unit of product? Are there any opportunities to reduce costs?
Once you've evaluated your current manufacturing processes, you can begin to identify where ERP could make a difference. Perhaps you need a more efficient way to track inventory or want to streamline order fulfillment. Maybe you need better visibility into production costs or want to improve communication between departments. Whatever your specific needs may be, understanding your current processes is essential for implementing ERP successfully.
Selecting the Right ERP System
The most crucial factor to consider when looking for an ERP system to support your manufacturing business is the tight integration of the software modules. Having a system that will allow easy integration with your current accounting, customer relationship management (CRM), and enterprise resource planning (ERP) software is vital.
Many off-the-shelf solutions offer tight integration, but it is indispensable to consider the costs associated with these options. Some vendors will provide a comprehensive manufacturing solution that includes all the necessary components for a successful implementation. These solutions can be expensive, but they offer the benefits of seamless integration and a lower total cost of ownership (TCO).
Conclusion
Enterprise Resource Planning (ERP) systems help manufacturers manage the production process by integrating various departments and functions into a single software application. ERP systems for Manufacturing typically include accounting, supply chain management, quality control, and shipping and receiving modules.
There are many benefits to implementing an ERP system in a manufacturing business. ERP systems can improve communication and collaboration between departments, help companies to respond quickly to changes in customer demand, and reduce the time needed to complete tasks such as invoicing and inventory management. In addition, ERP systems can provide valuable data insights, which can be used to improve manufacturing processes.
However, some challenges are associated with implementing an ERP system in a manufacturing business. One challenge is that it can be difficult to find an ERP system that meets the specific needs of a manufacturing business. In addition, implementing an ERP system can be complex and time-consuming, and there is a risk of not partnering with the right platform.
If you are considering implementing an ERP system in your manufacturing business, it is important to research and carefully consider all potential benefits and challenges. Working with a partner with experience implementing ERP systems in manufacturing businesses can help you navigate these waters.
SIX ERP is a turnkey solution that will help you implement and streamline your production pipeline and can be used by most industries. With an effortless process, we can help your business to become more effective. Our Data Driven approach, combined with limitless connectivity, opens up new possibilities in a connected world. Talk to our consultants to learn more about SIX Enterprise Resource Planning Solutions.
About the author
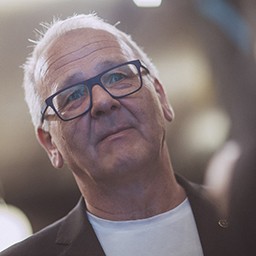
Andreas is a result-oriented CEO who brings nearly 30 years of experience gained in the high-tech industry. His experience ranges up to leading positions in Fortune 100 companies such as rentalcars.com (PCLN) or Intrasoft International, a leading EU based R&D software vendor. He holds a Ph.D. in Neural Networks from the University of Cologne, Germany.
In the past Andreas has successfully founded and co-founded several startups among others XXL Cloud Inc., eShopLeasing Ltd, and WDS Consulting SA. His expertise is strongly focused on modern headless Commerce and the optimization of processes in IT ecosystems.
Related articles
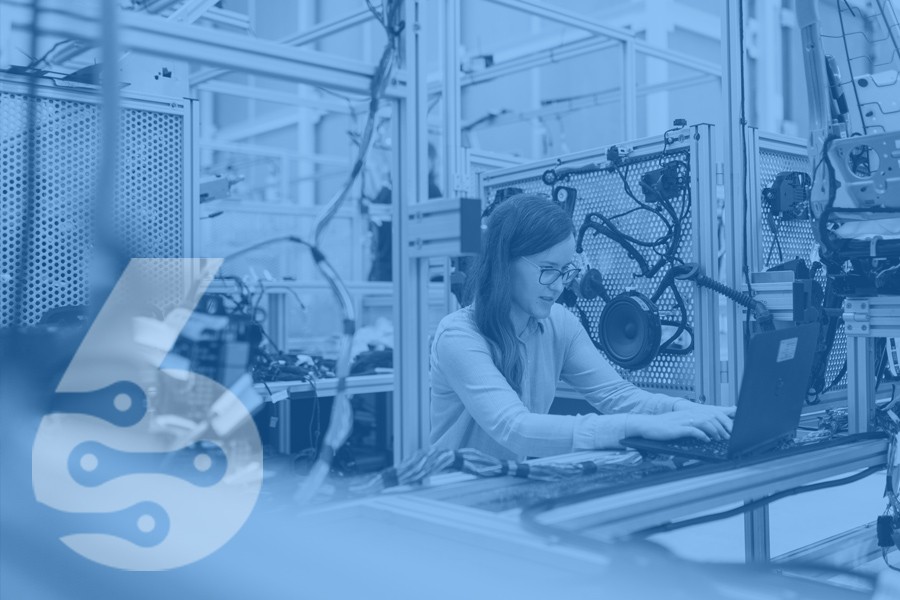
Implementing ERPs in manufacturing companies - Tips and Considerations
Are you considering implementing an ERP in your manufacturing company? It's a big decision, and there's much to consider. But don't worry - we're here to help. This blog post...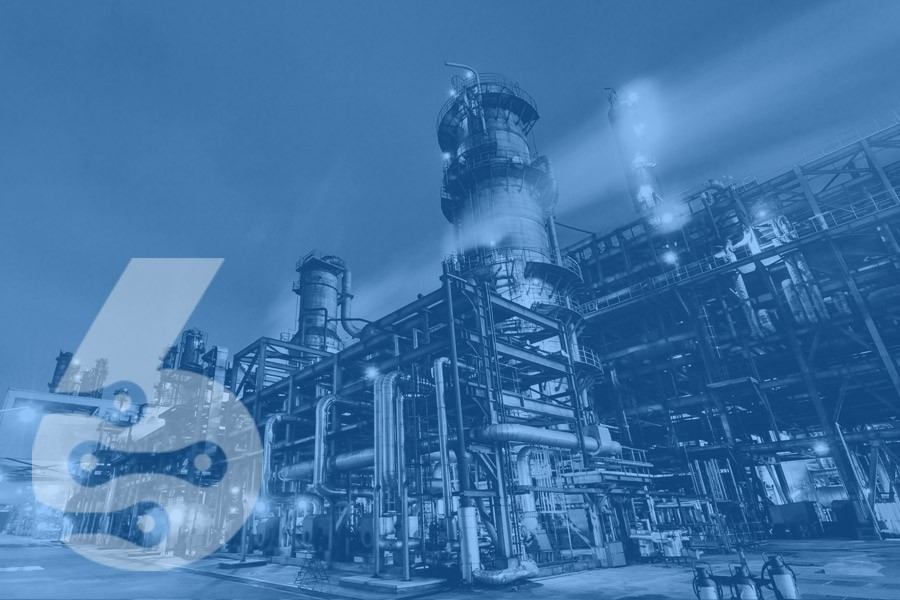
Top 20 Industries That Need ERP Systems The Most
ERP systems are essential for many businesses, but certain industries can benefit more from their use than others. ERP systems offer several advantages to companies, including increased efficiency, improved decision-making...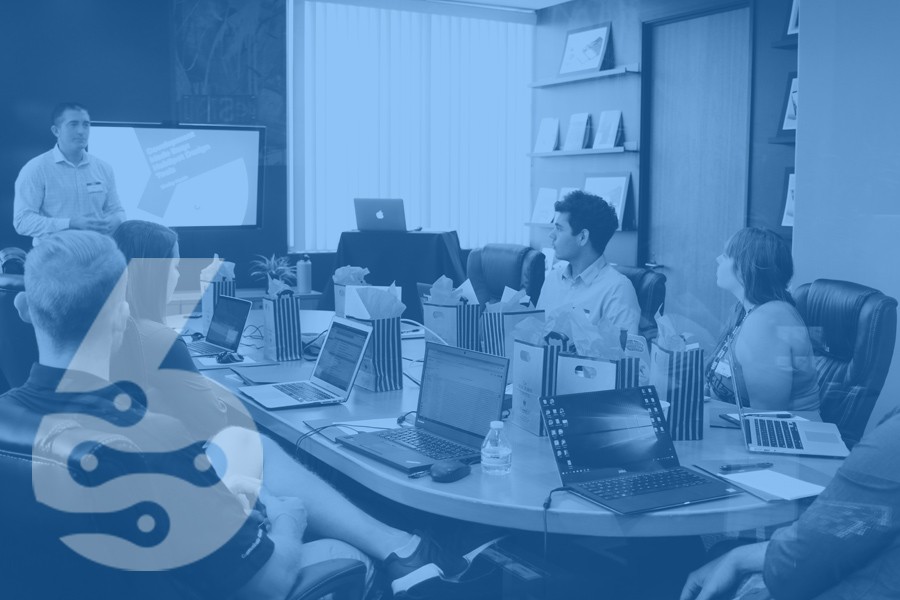